Steel detailing software is a computer-aided design (CAD) application used to create detailed drawings and models of steel structures. It allows engineers and detailers to accurately define the geometry, dimensions, and connections of steel members, such as beams, columns, and plates.
Steel detailing software has become an essential tool in the construction industry, streamlining the design process and improving accuracy. It enables engineers to optimize designs, reduce errors, and increase productivity. One significant historical development in this field was the introduction of 3D modeling capabilities, which provide a more comprehensive and realistic representation of steel structures.
In this article, we will explore the key features and benefits of steel detailing software, discuss its applications in various industries, and examine recent advancements and trends shaping its future.
Steel Detailing Software
Steel detailing software has become an indispensable tool in the construction industry, offering numerous benefits that streamline and enhance the design process. Key aspects of steel detailing software include:
- Accuracy
- Efficiency
- Collaboration
- 3D Modeling
- Automation
- Integration
- Customization
- Industry Standards
These aspects work together to create a comprehensive and powerful tool that enables engineers and detailers to deliver high-quality steel structures. For instance, the accuracy and efficiency of the software reduce errors and save time, while 3D modeling and collaboration features facilitate effective communication and coordination among project stakeholders. Furthermore, the integration with other design and analysis software ensures a seamless workflow and data consistency throughout the project lifecycle.
Accuracy
Accuracy is paramount in steel detailing, where even minor errors can have significant consequences for the safety and integrity of a structure. Steel detailing software plays a crucial role in achieving accuracy by providing a range of tools and features that minimize the risk of mistakes and ensure precision.
One key aspect is the use of parametric modeling, which allows engineers to define relationships between different elements of the steel structure. This means that when one element is modified, the software automatically updates all related elements, ensuring consistency and reducing the likelihood of errors. Additionally, steel detailing software typically includes extensive libraries of pre-defined shapes and connections, which have been thoroughly tested and verified. This reduces the need for manual calculations and eliminates potential sources of error.
Another important feature is the ability to perform real-time clash detection. This helps to identify potential conflicts between different components of the structure, such as overlapping beams or pipes. By addressing these clashes early in the design process, engineers can avoid costly and time-consuming rework during construction.
The accuracy provided by steel detailing software is essential for ensuring the safety and reliability of steel structures. It allows engineers to design and detail complex structures with confidence, knowing that the software is helping them to minimize errors and deliver high-quality results.
Efficiency
In the realm of steel detailing software, efficiency takes center stage, enabling engineers and detailers to streamline their workflows and maximize productivity. This efficiency manifests in several key facets:
- Automated Drafting: Steel detailing software automates repetitive drafting tasks, such as generating shop drawings, bills of materials, and NC files. This eliminates the need for manual drafting, saving countless hours and reducing the risk of errors.
- Parametric Modeling: Parametric modeling allows engineers to make changes to the design and have the software automatically update all related elements. This eliminates the need to manually update individual components, saving time and ensuring consistency throughout the design.
- Clash Detection: Steel detailing software can identify potential clashes between different components of the structure, such as overlapping beams or pipes. This helps to avoid costly and time-consuming rework during construction.
- Integration with Other Software: Steel detailing software can be integrated with other design and analysis software, such as structural analysis and finite element analysis (FEA) software. This allows for a seamless workflow and ensures data consistency throughout the project lifecycle.
By leveraging these efficiency-enhancing features, steel detailing software empowers engineers and detailers to deliver high-quality steel structures in a shorter amount of time. This efficiency not only translates to cost savings but also allows for more innovative and complex designs that would be difficult or impossible to achieve using manual methods.
Collaboration
Collaboration is a cornerstone of steel detailing software, enabling multiple stakeholders to work together seamlessly on complex steel structures. This collaborative approach streamlines the design process, reduces errors, and improves overall project outcomes.
- Real-Time Communication: Steel detailing software allows engineers, detailers, and fabricators to communicate and share project updates in real time. This eliminates delays and ensures that everyone is working with the most up-to-date information.
- Centralized Data Management: All project data is stored in a central location, accessible to all authorized users. This ensures that everyone has access to the same information, reducing the risk of errors and inconsistencies.
- Integrated Review and Approval: Steel detailing software provides tools for integrated review and approval of drawings and models. This streamlines the approval process and ensures that all stakeholders are on the same page.
- Enhanced Coordination: Steel detailing software facilitates better coordination between different disciplines, such as architecture, structural engineering, and fabrication. This helps to identify and resolve potential issues early on, avoiding costly rework and delays.
By fostering collaboration, steel detailing software empowers project teams to work together more efficiently and effectively. This leads to improved project outcomes, reduced costs, and increased client satisfaction.
3D Modeling
3D modeling has revolutionized the field of steel detailing, becoming an indispensable component of modern steel detailing software. It allows engineers and detailers to create realistic and accurate digital representations of steel structures, enabling them to visualize and analyze designs with unprecedented clarity and precision.
The integration of 3D modeling into steel detailing software has had a profound impact on the design process. It has streamlined workflows, improved collaboration, and reduced errors. Engineers can now create complex steel structures with ease, exploring different design options and optimizing their designs for efficiency and cost-effectiveness. 3D modeling also facilitates communication and collaboration among project stakeholders, as it provides a common platform for visualizing and discussing design concepts.
Real-life examples of 3D modeling in steel detailing software abound. For instance, the Burj Khalifa, the world’s tallest building, was designed using 3D modeling software. The software allowed the engineers to create a detailed virtual model of the building, which they used to optimize the structural design and identify potential construction challenges. Similarly, the Sydney Opera House was redesigned using 3D modeling software, enabling the architects to explore different design options and visualize the building’s complex geometry.
The practical applications of 3D modeling in steel detailing software extend far beyond these high-profile examples. It is used in a wide range of industries, including commercial construction, industrial fabrication, and bridge design. By providing a comprehensive and immersive view of steel structures, 3D modeling helps engineers and detailers to make informed decisions, reduce errors, and deliver high-quality projects on time and within budget.
Automation
Automation is a transformative aspect of steel detailing software, revolutionizing the way engineers and detailers approach the design and detailing of steel structures. It encompasses a range of technologies and features that streamline workflows, reduce errors, and enhance productivity.
- Automated Drafting: This feature automates the creation of shop drawings, bills of materials, and NC files, eliminating repetitive tasks and saving countless hours. It ensures consistency and accuracy, reducing the risk of errors.
- Parametric Modeling: Parametric modeling allows engineers to define relationships between different elements of the steel structure. When one element is modified, the software automatically updates all related elements, ensuring consistency and saving time.
- Clash Detection: Automation includes real-time clash detection, which identifies potential conflicts between different components of the structure, such as overlapping beams or pipes. This helps to avoid costly and time-consuming rework during construction.
- Code Compliance Checking: Steel detailing software can automatically check designs for compliance with building codes and standards. This helps to ensure that structures meet safety and performance requirements, reducing the risk of costly rework or legal issues.
Automation in steel detailing software empowers engineers and detailers to work more efficiently and effectively. It reduces the time and effort required to complete projects, while also improving accuracy and consistency. This leads to cost savings, reduced errors, and improved project outcomes.
Integration
Integration is a critical aspect of steel detailing software, as it enables seamless communication and data exchange between different software applications and systems. This integration streamlines workflows, reduces errors, and enhances the overall efficiency of the steel detailing process.
One key integration is between steel detailing software and structural analysis software. This integration allows engineers to transfer structural analysis models directly into the detailing software, ensuring that the detailing is accurate and consistent with the structural design. Additionally, integration with fabrication management software enables the automatic generation of cut lists, nesting plans, and other fabrication-related documents, reducing the risk of errors and saving time.
Real-life examples of integration in steel detailing software include the integration of Tekla Structures with Autodesk Revit and the integration of SDS/2 with AutoCAD. These integrations allow engineers and detailers to work with familiar software platforms while leveraging the specialized capabilities of each application. By seamlessly transferring data between different software systems, integration eliminates the need for manual data entry and reduces the risk of errors.
In summary, integration is a vital component of steel detailing software, enabling efficient workflows, accurate detailing, and improved collaboration among project stakeholders. It reduces errors, saves time, and enhances the overall quality of steel detailing projects.
Customization
Customization is a fundamental aspect of steel detailing software, enabling engineers and detailers to tailor the software to meet their specific needs and preferences. This customization empowers them to create bespoke solutions that streamline workflows, enhance productivity, and improve the quality of their detailing work.
- Customizable Templates: Steel detailing software allows users to create and modify templates for various drawing types, such as shop drawings, fabrication details, and erection plans. These templates can include company-specific standards, predefined symbols, and automated detailing rules, saving time and ensuring consistency.
- Adaptable User Interface: Modern steel detailing software provides customizable user interfaces that can be tailored to individual preferences. Engineers and detailers can modify toolbars, create custom shortcuts, and adjust the layout of the software to suit their working style, enhancing efficiency and comfort.
- Integration with External Applications: Steel detailing software can be customized to integrate with other software applications, such as structural analysis software, project management tools, and fabrication equipment. This integration allows for seamless data exchange and automated workflows, reducing errors and improving overall project coordination.
- Scriptable Functionality: Advanced steel detailing software offers scriptable functionality, allowing users to create custom scripts and macros to automate repetitive tasks or extend the software’s capabilities. This level of customization empowers engineers and detailers to develop tailored solutions that meet the unique requirements of their projects.
In summary, customization is a key feature of steel detailing software that empowers engineers and detailers to tailor the software to their specific needs and preferences. Through customizable templates, adaptable user interfaces, integration with external applications, and scriptable functionality, steel detailing software becomes a versatile and powerful tool that enhances productivity, improves accuracy, and streamlines the entire steel detailing process.
Industry Standards
Industry standards play a critical role in the development and implementation of steel detailing software. These standards provide a common set of guidelines and best practices that ensure the accuracy, consistency, and interoperability of steel detailing data. By adhering to industry standards, steel detailing software can effectively meet the requirements of engineers, fabricators, and other stakeholders involved in steel construction projects.
One of the key benefits of industry standards in steel detailing software is the promotion of data accuracy and consistency. Standardized data formats and detailing conventions facilitate seamless data exchange between different software applications and systems, reducing the risk of errors and misinterpretations. This is particularly important in complex steel structures where accurate detailing is essential for structural integrity and safety.
Real-life examples of industry standards in steel detailing software include the American Institute of Steel Construction (AISC) standards and the European Committee for Standardization (CEN) standards. These standards provide comprehensive guidelines for the design, detailing, and fabrication of steel structures. Steel detailing software that conforms to these standards ensures that the generated drawings and models meet industry best practices and comply with relevant building codes and regulations.
The practical applications of industry standards in steel detailing software extend beyond data accuracy and consistency. Standardized detailing practices improve communication and collaboration among project stakeholders. Engineers, detailers, and fabricators can work with confidence knowing that they are using a common language and following the same conventions. This reduces the potential for miscommunication and errors, ultimately leading to improved project outcomes and reduced costs.
FAQs on Steel Detailing Software
This section addresses frequently asked questions and clarifies common misconceptions about steel detailing software. These FAQs provide valuable insights into the capabilities, benefits, and applications of this essential tool in the steel construction industry.
Question 1: What is steel detailing software used for?
Answer: Steel detailing software is a specialized computer-aided design (CAD) tool used to create detailed drawings and models of steel structures. It enables engineers and detailers to accurately define the geometry, dimensions, and connections of steel members, such as beams, columns, and plates.
Question 2: What are the benefits of using steel detailing software?
Answer: Steel detailing software offers numerous benefits, including improved accuracy and efficiency, enhanced collaboration, advanced 3D modeling capabilities, automated detailing tasks, seamless integration with other software, and customization options tailored to specific project requirements.
Question 3: How does steel detailing software improve accuracy?
Answer: Steel detailing software utilizes parametric modeling, extensive libraries of pre-defined shapes and connections, and real-time clash detection to minimize errors and ensure the precision of steel detailing drawings and models.
Question 4: How does steel detailing software enhance collaboration?
Answer: Steel detailing software facilitates effective collaboration among project stakeholders by enabling real-time communication, centralized data management, integrated review and approval processes, and enhanced coordination between different disciplines.
Question 5: What are the practical applications of 3D modeling in steel detailing software?
Answer: 3D modeling in steel detailing software allows for the creation of realistic and accurate digital representations of steel structures. It enables engineers and detailers to visualize and analyze designs with greater clarity, optimize structural efficiency, and facilitate communication and coordination among project stakeholders.
Question 6: How does steel detailing software integrate with other software?
Answer: Steel detailing software can be integrated with structural analysis software, fabrication management software, and other design and engineering applications. This integration streamlines workflows, reduces errors, and enhances the overall efficiency of the steel detailing process.
These FAQs offer a comprehensive overview of the key aspects of steel detailing software. Its accuracy, efficiency, collaboration-enhancing features, advanced 3D modeling capabilities, and integration options make it an indispensable tool in the steel construction industry. As we delve deeper into the article, we will explore specific examples and case studies to further illustrate the practical applications and transformative impact of steel detailing software in real-world projects.
Tips for Effective Steel Detailing
In this section, we present practical tips to help engineers and detailers optimize their steel detailing workflows and deliver high-quality results. By implementing these tips, professionals can enhance accuracy, efficiency, and collaboration in their steel detailing projects.
Tip 1: Utilize Parametric Modeling: Leverage parametric modeling capabilities to define relationships between elements, ensuring consistency and reducing the risk of errors during design modifications.
Tip 2: Establish Clear Standards: Implement and adhere to company or industry standards for detailing practices, symbols, and conventions to promote consistency and minimize misinterpretation.
Tip 3: Employ Automation Features: Take advantage of automated drafting, clash detection, and code compliance checking tools to streamline workflows, reduce errors, and enhance productivity.
Tip 4: Foster Collaboration and Communication: Establish clear communication channels and protocols among engineers, detailers, and fabricators to ensure timely and accurate information exchange.
Tip 5: Utilize 3D Modeling for Visualization: Create 3D models to visualize and analyze steel structures, improving design optimization, clash detection, and communication with project stakeholders.
Tip 6: Integrate with Other Software: Integrate steel detailing software with structural analysis and fabrication management software to streamline workflows, reduce data re-entry, and enhance overall project coordination.
Tip 7: Regularly Review and Update Standards: Stay updated with the latest industry standards and best practices for steel detailing to ensure compliance and continuous improvement.
Tip 8: Seek Professional Development Opportunities: Attend workshops, training sessions, and conferences to expand knowledge and skills in steel detailing software and industry trends.
By implementing these tips, engineers and detailers can harness the full potential of steel detailing software. These practices promote accuracy, efficiency, collaboration, and continuous improvement, ultimately leading to successful and high-quality steel detailing projects.
In the concluding section, we will discuss emerging trends and advancements in steel detailing software and their impact on the future of the industry.
Conclusion
In this comprehensive exploration of steel detailing software, we have examined its multifaceted role in revolutionizing the steel construction industry. Key insights emerged throughout our investigation, highlighting the profound impact of this technology on accuracy, efficiency, collaboration, and overall project outcomes.
Three main points stand out as interconnected pillars of steel detailing software’s transformative power:
- Precision and Automation: Parametric modeling, clash detection, and automated detailing tasks minimize errors and enhance productivity.
- Enhanced Collaboration: Real-time communication, centralized data management, and integrated review processes foster seamless collaboration among project stakeholders.
- Integration and Customization: Seamless integration with other software and customizable features adapt the software to specific project requirements.
As the future of steel detailing software unfolds, we anticipate further advancements in automation, artificial intelligence, and cloud-based solutions. These innovations will empower engineers and detailers to push the boundaries of design and construction, unlocking even greater efficiency and accuracy in the delivery of steel structures. Embracing these advancements will be key to unlocking the full potential of steel detailing software and shaping the future of the steel construction industry.
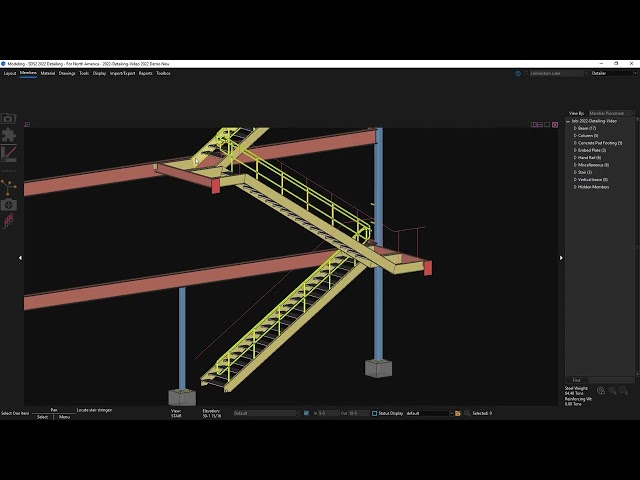