Factory Acceptance Test Software: A Comprehensive Overview
Factory Acceptance Test (FAT) software is a specialized tool designed to facilitate the testing and validation of industrial equipment and systems before their installation at the end-user’s site. For instance, in the manufacturing industry, FAT software is used to evaluate the functionality of production lines before they are shipped to the production facility.
FAT software streamlines the testing process, enhances accuracy, and ensures that equipment meets specifications and operates seamlessly. It has gained significant prominence in recent years due to its ability to detect defects early on, reducing costly rework and potential safety hazards. Historically, FAT was performed manually, but the advent of dedicated software has revolutionized the process, introducing automation, data analysis, and comprehensive reporting.
This article delves deeper into the world of FAT software, exploring its principles, benefits, applications, and key considerations. We will also discuss best practices and emerging trends that are shaping the future of factory acceptance testing.
Factory Acceptance Test Software
Factory acceptance test (FAT) software plays a crucial role in ensuring the quality and reliability of industrial equipment and systems before their installation at the end-user’s site. Key aspects of FAT software include:
- Automation: Streamlining testing processes, saving time and resources.
- Accuracy: Enhancing the precision and reliability of test results.
- Documentation: Generating detailed reports for traceability and compliance.
- Integration: Facilitating seamless integration with other testing tools and systems.
- Customization: Tailoring tests to specific equipment and system requirements.
- Data analysis: Providing insights into test results for informed decision-making.
- Collaboration: Enabling collaboration among stakeholders throughout the testing process.
- Compliance: Ensuring adherence to industry standards and regulatory requirements.
These aspects are interconnected and contribute to the overall effectiveness of FAT software. For example, automation reduces testing time, while accuracy ensures reliable results. Customization allows for tailored testing, and data analysis provides valuable insights for improving equipment design and performance. Compliance ensures that equipment meets industry standards, while collaboration facilitates efficient communication among stakeholders. Together, these aspects enhance the quality and reliability of industrial equipment and systems, ensuring their smooth operation and minimizing the risk of costly rework or failures.
Automation
Automation is a critical component of factory acceptance test (FAT) software. By automating testing processes, FAT software significantly reduces testing time and saves valuable resources. Manual testing, which involves human operators physically performing each test, can be time-consuming and prone to errors. In contrast, automated testing uses software to execute tests, eliminating the need for manual intervention and reducing the likelihood of human error. This automation leads to faster testing cycles, allowing manufacturers to quickly identify and address any issues with their equipment or systems before they are shipped to the end-user’s site.
For example, in the automotive industry, FAT software is used to test the functionality of various vehicle components, such as engines, transmissions, and electrical systems. Automated testing enables manufacturers to conduct comprehensive tests on multiple vehicles simultaneously, significantly reducing the time required to complete the testing process. This efficiency allows manufacturers to increase their production output and meet customer demand more quickly.
The practical applications of automation in FAT software extend beyond the automotive industry. In the manufacturing sector, FAT software is used to test production lines and other complex machinery. Automation enables manufacturers to simulate real-world operating conditions and thoroughly evaluate the performance of their equipment before it is installed at the end-user’s site. This proactive approach helps to identify and resolve potential issues early on, reducing the risk of costly downtime and production delays.
In conclusion, automation is a crucial aspect of factory acceptance test software. By streamlining testing processes and saving time and resources, automation enhances the efficiency and effectiveness of FAT procedures. Automated testing reduces the likelihood of human error, increases testing speed, and facilitates the identification and resolution of issues early in the manufacturing process. The benefits of automation translate into improved product quality, reduced production costs, and increased customer satisfaction.
Accuracy
Accuracy is a critical aspect of factory acceptance test (FAT) software. It ensures the precision and reliability of test results, which are essential for evaluating the quality and performance of industrial equipment and systems. Accurate test results provide manufacturers with the confidence that their products meet specifications and will operate flawlessly in the field. Without accurate testing, manufacturers risk releasing defective products that could lead to costly rework, production delays, and damage to their reputation.
FAT software achieves accuracy through a combination of sophisticated algorithms, data analysis techniques, and rigorous testing procedures. The software is designed to minimize the influence of external factors, such as environmental conditions or human error, on test results. Automated testing eliminates the possibility of human error and ensures consistent testing conditions, further enhancing accuracy. Additionally, FAT software often incorporates self-checking mechanisms to verify the accuracy of its own test procedures.
Real-life examples of accuracy in FAT software abound. In the aerospace industry, FAT software is used to test the functionality of critical aircraft components, such as flight control systems and navigation equipment. Accurate testing is essential to ensure the safety and reliability of aircraft, as any errors in the test results could have catastrophic consequences. In the medical device industry, FAT software is used to test the performance of life-saving equipment, such as pacemakers and surgical robots. Accurate testing is crucial to ensure that these devices function properly and do not put patients at risk.
The practical applications of accuracy in FAT software extend beyond these specific industries. Accurate testing is essential for any industry that relies on complex equipment and systems to operate safely and efficiently. By providing precise and reliable test results, FAT software helps manufacturers identify and resolve potential issues early in the manufacturing process, reducing the risk of costly rework and production delays. Accurate testing also contributes to increased product quality, customer satisfaction, and brand reputation.
In summary, accuracy is a critical component of factory acceptance test software. It ensures the precision and reliability of test results, which are essential for evaluating the quality and performance of industrial equipment and systems. Accurate testing helps manufacturers identify and resolve potential issues early in the manufacturing process, reducing the risk of costly rework and production delays. It also contributes to increased product quality, customer satisfaction, and brand reputation.
Documentation
In the realm of factory acceptance test (FAT) software, documentation plays a crucial role in ensuring traceability and compliance. Detailed reports generated by FAT software provide a comprehensive record of the testing process, enabling manufacturers to track the progress of testing, identify any issues that arise, and demonstrate compliance with industry standards and regulatory requirements.
- Test Specifications: FAT software generates detailed test specifications that outline the specific tests to be performed, the acceptance criteria, and the equipment and materials required. These specifications serve as a roadmap for the testing process and ensure that all necessary tests are conducted.
- Test Results: FAT software records the results of each test, including pass/fail status, any deviations from the acceptance criteria, and any observations made during testing. These records provide a complete picture of the equipment’s performance and help identify areas for improvement.
- Traceability: FAT software enables traceability throughout the testing process. Each test result is linked to the specific test specification and the equipment under test. This traceability allows manufacturers to easily identify the source of any issues and trace the testing history of each piece of equipment.
- Compliance Reporting: FAT software generates comprehensive reports that document the testing process and the equipment’s performance. These reports can be used to demonstrate compliance with industry standards and regulatory requirements, such as ISO 9001 or FDA regulations.
The detailed reports generated by FAT software are essential for ensuring the quality and reliability of industrial equipment and systems. They provide manufacturers with the documentation they need to trace the testing process, identify any issues, and demonstrate compliance with industry standards and regulations. Ultimately, this documentation contributes to increased product quality, reduced risk, and enhanced customer confidence.
Integration
Within the realm of factory acceptance test (FAT) software, integration plays a crucial role in streamlining and enhancing the testing process. By seamlessly integrating with other testing tools and systems, FAT software enables a comprehensive and efficient approach to equipment and system testing.
- Data Exchange: FAT software seamlessly exchanges data with other testing tools and systems, ensuring a unified testing environment. This data exchange eliminates the need for manual data entry and reduces the risk of errors, enhancing the overall accuracy and efficiency of the testing process.
- Test Automation: Integration with test automation frameworks allows FAT software to automate repetitive testing tasks, saving time and resources. Automated tests can be executed on multiple devices and systems simultaneously, increasing testing coverage and reducing the overall testing time.
- Defect Tracking: FAT software integrates with defect tracking systems, enabling the seamless reporting and tracking of defects identified during testing. This integration facilitates efficient defect management and resolution, ensuring that issues are addressed promptly and effectively.
- Compliance Management: FAT software can integrate with compliance management systems to ensure that testing processes and documentation meet industry standards and regulatory requirements. This integration helps streamline compliance audits and demonstrates the organization’s commitment to quality and safety.
The seamless integration of FAT software with other testing tools and systems offers numerous benefits. It enhances the efficiency and accuracy of the testing process, reduces testing time, and facilitates comprehensive defect management and compliance. By integrating with a variety of tools and systems, FAT software provides a holistic and streamlined approach to factory acceptance testing, ensuring the quality and reliability of industrial equipment and systems.
Customization
In the realm of factory acceptance test (FAT) software, customization plays a pivotal role in ensuring that tests are tailored to the unique requirements of specific equipment and systems. This customization is critical because it enables manufacturers to conduct comprehensive and accurate testing that accurately reflects the intended use and operating environment of their products.
FAT software provides a range of customization options that allow manufacturers to define specific test parameters, sequences, and acceptance criteria. This flexibility ensures that tests are tailored to the specific functionality, performance, and safety requirements of each piece of equipment or system. By customizing tests, manufacturers can identify and address potential issues early in the manufacturing process, reducing the risk of costly rework and production delays.
Real-life examples of customization in FAT software abound. In the automotive industry, FAT software is used to test the functionality of various vehicle components, such as engines, transmissions, and electrical systems. Customization allows manufacturers to tailor tests to the specific vehicle model, engine type, and transmission configuration. This ensures that each component is thoroughly tested under conditions that simulate real-world operating scenarios.
The practical applications of customization in FAT software extend beyond the automotive industry. In the manufacturing sector, FAT software is used to test production lines and other complex machinery. Customization enables manufacturers to simulate specific production processes and evaluate the performance of their equipment under varying operating conditions. This proactive approach helps to identify and resolve potential issues early on, reducing the risk of costly downtime and production delays.
In summary, customization is a critical component of factory acceptance test software. It allows manufacturers to tailor tests to the specific requirements of their equipment and systems, ensuring comprehensive and accurate testing. By identifying and addressing potential issues early in the manufacturing process, customization contributes to increased product quality, reduced production costs, and enhanced customer satisfaction.
Data analysis
Data analysis is a critical component of factory acceptance test (FAT) software. It enables manufacturers to extract valuable insights from test results, which are essential for making informed decisions about the quality and performance of their equipment and systems. Advanced data analysis techniques provide manufacturers with a deeper understanding of how their products behave under various operating conditions and identify areas for improvement.
Real-life examples of data analysis in FAT software are numerous. In the automotive industry, FAT software is used to test the functionality of various vehicle components, such as engines, transmissions, and electrical systems. Data analysis enables manufacturers to identify patterns and trends in test results, which can indicate potential issues or areas for optimization. This information helps manufacturers make informed decisions about design modifications or production processes to improve the overall quality and performance of their vehicles.
The practical applications of data analysis in FAT software extend beyond the automotive industry. In the manufacturing sector, FAT software is used to test production lines and other complex machinery. Data analysis enables manufacturers to monitor equipment performance over time, identify potential maintenance issues, and optimize production processes. This proactive approach helps manufacturers reduce downtime, increase productivity, and improve the overall efficiency of their operations.
In summary, data analysis is a critical component of factory acceptance test software. It provides manufacturers with valuable insights into the quality and performance of their equipment and systems. By analyzing test results, manufacturers can identify potential issues, optimize production processes, and make informed decisions to improve the overall quality and reliability of their products.
Collaboration
Collaboration is a critical component of factory acceptance test (FAT) software. It enables stakeholders from various departments, such as engineering, manufacturing, and quality assurance, to work together seamlessly throughout the testing process. This collaborative approach ensures that all relevant perspectives and expertise are considered, leading to more comprehensive and effective testing.
Factory acceptance test software facilitates collaboration by providing a centralized platform for stakeholders to share information, track progress, and discuss test results. Real-time communication features, such as instant messaging and video conferencing, enable stakeholders to quickly resolve issues and make informed decisions. Additionally, FAT software provides tools for version control and document management, ensuring that all stakeholders have access to the most up-to-date information.
Practical applications of collaboration in FAT software abound. In the manufacturing industry, FAT software is used to test complex machinery and production lines. Collaboration among stakeholders ensures that all aspects of the equipment are thoroughly tested, from functionality and safety to performance and reliability. This collaborative approach helps manufacturers identify and resolve potential issues early in the manufacturing process, reducing the risk of costly rework and production delays.
In conclusion, collaboration is a critical component of factory acceptance test software. It enables stakeholders from various departments to work together effectively, ensuring comprehensive and efficient testing. By fostering collaboration, FAT software contributes to increased product quality, reduced production costs, and enhanced customer satisfaction.
Compliance
Within the realm of factory acceptance test (FAT) software, compliance plays a critical role in ensuring that equipment and systems meet industry standards and regulatory requirements. Adherence to these standards is paramount for various reasons, including safety, quality, and legal liability.
-
Industry Standards:
FAT software helps manufacturers comply with industry-specific standards, such as ISO 9001 for quality management or IEC 61508 for functional safety. Adhering to these standards demonstrates a commitment to quality and safety, enhancing customer confidence and reducing the risk of product recalls or liability issues.
-
Regulatory Requirements:
In certain industries, such as medical devices or aerospace, compliance with regulatory requirements is mandatory. FAT software assists manufacturers in meeting these requirements, ensuring that equipment and systems meet the necessary safety and performance criteria. This compliance helps avoid legal penalties, product bans, or reputational damage.
-
Legal Liability:
FAT software provides documentation and traceability throughout the testing process, which is essential in the event of product liability claims. Detailed test reports and records serve as evidence of compliance with standards and regulations, helping manufacturers defend against legal challenges and protect their reputation.
-
Customer Confidence:
Customers increasingly demand products that meet or exceed industry standards and regulatory requirements. FAT software enables manufacturers to demonstrate compliance, building trust and confidence among customers. This can lead to increased sales, customer loyalty, and a positive reputation in the marketplace.
Compliance, therefore, is not merely a legal obligation but a strategic imperative for manufacturers. By leveraging FAT software to ensure adherence to industry standards and regulatory requirements, manufacturers can enhance product quality, reduce risk, and gain a competitive advantage in the global marketplace.
Frequently Asked Questions (FAQs) on Factory Acceptance Test Software
This section addresses common queries and clarifies key aspects of factory acceptance test (FAT) software:
Question 1: What is the primary purpose of FAT software?
Answer: FAT software automates and streamlines the testing of industrial equipment and systems before they are shipped to the end-user’s site. It enhances accuracy and efficiency, ensuring that equipment meets specifications and operates seamlessly.
Question 2: What are the benefits of using FAT software?
Answer: FAT software offers numerous benefits, including reduced testing time, enhanced accuracy, comprehensive documentation, seamless integration with other testing tools, customization to specific testing requirements, and data analysis for informed decision-making.
Question 3: How does FAT software ensure compliance with industry standards and regulations?
Answer: FAT software provides features such as traceability, detailed reporting, and adherence to industry-specific standards. This ensures that equipment meets the necessary safety and performance criteria, minimizing legal risks and enhancing customer confidence.
Question 4: Is FAT software suitable for all industries?
Answer: FAT software is applicable to various industries, including manufacturing, automotive, aerospace, and medical devices. It is particularly beneficial for testing complex equipment and systems that require rigorous testing before deployment.
Question 5: How does FAT software facilitate collaboration among stakeholders?
Answer: FAT software provides a centralized platform for stakeholders from different departments to share information, track progress, and discuss test results. This collaboration ensures that all perspectives are considered, leading to more comprehensive and effective testing.
Question 6: What are the key considerations when selecting FAT software?
Answer: When selecting FAT software, consider factors such as the specific testing requirements, the level of automation desired, the need for compliance with industry standards, the size and complexity of the equipment being tested, and the budget and resources available.
These FAQs provide insights into the key aspects and benefits of factory acceptance test software. In the next section, we will delve deeper into the implementation and best practices of FAT software to optimize testing processes and ensure the quality and reliability of industrial equipment and systems.
Transition to the next article section: Implementation and Best Practices of Factory Acceptance Test Software
Tips for Effective Factory Acceptance Testing
This section provides practical tips to enhance the efficiency and effectiveness of factory acceptance testing (FAT):
Tip 1: Plan Thoroughly: Define clear test objectives, identify required resources, and establish a comprehensive test plan to ensure systematic and organized testing.
Tip 2: Leverage Automation: Utilize FAT software to automate repetitive tasks, reduce testing time, and minimize human error, leading to increased accuracy and efficiency.
Tip 3: Foster Collaboration: Establish effective communication channels and encourage collaboration among stakeholders from various departments to ensure a shared understanding of testing requirements and seamless execution.
Tip 4: Ensure Equipment Readiness: Verify that the equipment under test is fully assembled, calibrated, and meets all necessary specifications before commencing testing to avoid delays or inaccurate results.
Tip 5: Conduct Environmental Testing: Simulate real-world operating conditions, including temperature, humidity, and vibration, to evaluate equipment performance under various environmental stresses.
Tip 6: Focus on Critical Functions: Prioritize testing of essential functions and safety features to ensure that the equipment operates as intended and meets critical performance criteria.
Tip 7: Document Thoroughly: Maintain detailed records of test procedures, results, and any deviations encountered. This documentation serves as evidence of compliance, facilitates troubleshooting, and enables continuous improvement.
Tip 8: Utilize Data Analysis: Leverage data analysis techniques to identify trends, patterns, and areas for improvement in the testing process and equipment performance.
Implementing these tips can significantly enhance the quality and reliability of factory acceptance testing. By following these best practices, manufacturers can optimize testing processes, reduce risks, and ensure that their equipment meets or exceeds customer expectations.
Transition to the article’s conclusion: By adopting these proven tips, businesses can transform factory acceptance testing into a strategic advantage, fostering customer confidence, minimizing production delays, and driving overall business success.
Conclusion
This comprehensive exploration of factory acceptance test (FAT) software has illuminated its significance in ensuring the quality and reliability of industrial equipment and systems. Key insights include the automation of testing processes, leading to increased efficiency and accuracy; the seamless integration with other testing tools and systems, enabling a comprehensive testing environment; and the facilitation of collaboration among stakeholders, ensuring a shared understanding and effective execution of testing.
As the manufacturing industry continues to evolve, FAT software will play an increasingly critical role. By embracing the advanced features and capabilities of FAT software, manufacturers can optimize their testing processes, reduce risks, and enhance the quality of their products. The adoption of FAT software is not merely a technological upgrade but a strategic investment in the long-term success and competitiveness of any manufacturing enterprise.
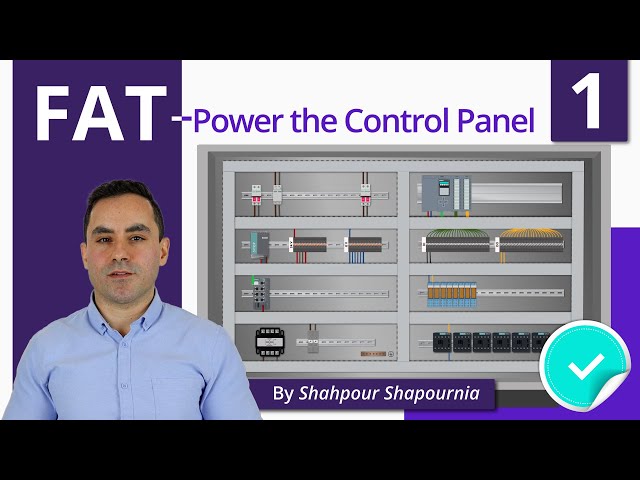